In diesem Video lernst du, wie du Bestandsoptimierung in 3 einfachen Schritten umsetzen kannst.
Bestandsoptimierung Prozessübersicht
Der Prozess der Lagerbestandsoptimierung läuft in 3 Schritten ab. Dem Demand Forecasting, der Inventory Optimization und dem Stock Replenishment.
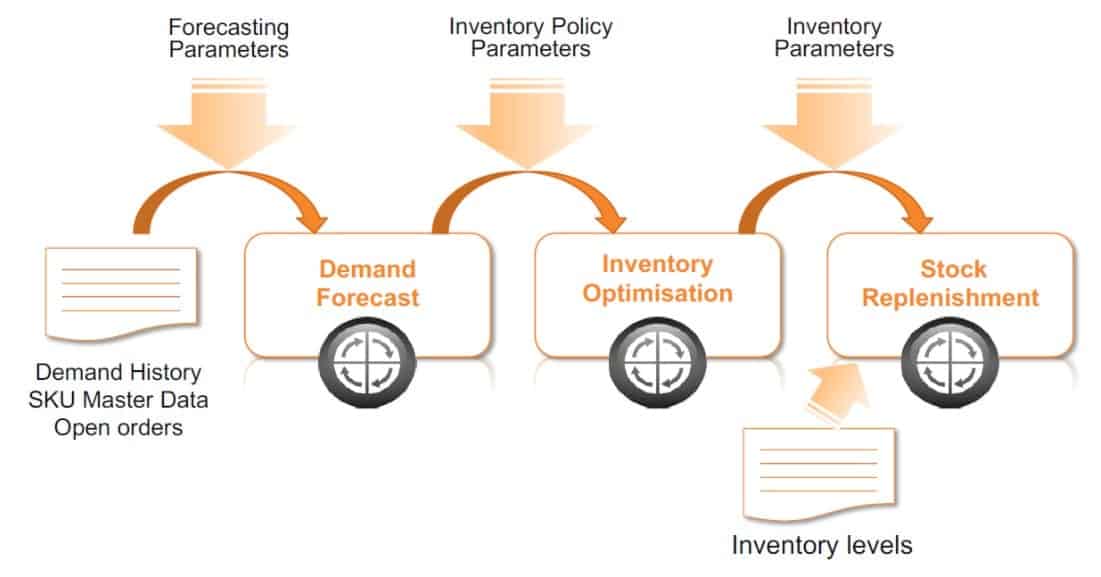
Jeder Schritt basierd dabei auf den Daten und Ergebnissen des vorhergehenden Schrittes.
Vereinfacht gesagt muss ich zunächst wissen wieviele Stück von einem Artikel in Zukunft benötigt werden, damit ich dies danach mit meinem aktuellen Bestand im Lager abgleichen kann, und danach entsprechende Bestellungen bei Lieferanten durchführen kann, um die fehlenden Mengen auszugleichen.
Schritt 1: Demand Forecasting
Der erste Schritt im Prozess ist das Forecasting. Hierbei geht es darum Vorhersagen für die zukünftigen Nachfragemengen von Artikeln zu erhalten.
Nur wenn man ein Bild über die zukünftigen Nachfragemengen der Artikel hat, kann man auch entsprechend handeln.
Diese Forecasts basieren dabei auf den historischen Verkaufszahlen (auch bekannt als "Bedarfe") aus der Vergangenheit. Dabei gilt es vor allem auch Trends und Saisonalitäten zu erkennen.
Viele System verwenden für die Berechnung der Forecasts ein und diesselbe statistische Methode für alle Artikel im Sortiment.
Dies kann allerdings zu Problemen führen, da es Artikel mit unterschiedlichen Mustern in der Nachfrage gibt. Beispielsweise gibt es Artikel welche sich nur sporadisch verkaufen, die einen positiven Trend haben oder welche, die eine hohe Schwankungsbreite in der Nachfrage haben.
Für diese unterschiedlichen Arten von Artikeln, im Fachjargon auch Bedarfsmuster genannt, braucht man auch unterschiedliche statistische Prognoseverfahren, damit man gute Forecasts erhält.
Eine andere Möglichkeit, wie man diese unterschiedlichen Bedarfsmuster von Artikeln betrachten kann, ist der Lebenszyklus eines Artikels. Je nachdem ob er gerade neu ins Sortiment kommt, und es damit noch keine Verkaufsdaten aus der Vergangenheit gibt, ob er sich gut verkauft, einen negativen Trend oder kurz vor dem Ausscheiden aus dem Sortiment ist, muss ich unterschiedliche Verfahren verwenden um gute Forecasts berechnen zu können.
Nähere Details zu den unterschiedlichen Bedarfsmustern und den Lebenszyklus eines Artikels erfährst du bald in einem eigenen Video.
Ein gutes Forecasting System muss auch in der Lage sein bereits bekannte zukünftige Nachfragen, z.B. von einer geplanten Werbekampagne, ebenfalls berücksichtigen zu können.
Wurde das Forecasting erfolgreich durchgeführt, ist die Datenbasis vorhanden mit der im nächsten Schritt dann die eigentliche Bestandsoptimierung durchgeführt werden kann.
Praxis Demand Forecasting
Pfuh, das war jetzt eine ganze Menge Theorie oder?
Schauen wir uns das Ganze anhand unseres fiktiven Unternehmens der "Lederhosen AG" an. Die Lederhosen AG ist ein mittelständisches Traditionsunternehmen und produziert und verkauft Trachtenmode wie Lederhosen und Dirndln. Dabei gilt es die hauseigenen Laden-Geschäfte sowie den Online Shop und Händler mit Produkten zu versorgen.
Die Lederhosen AG hat festgestellt, dass das Lager aus allen Nähten platzt und daher ein neues Bestandsoptimierungssystem eingeführt, damit der Lagerbestand so weit wie möglich reduziert wird.
Das Forecasting dieses neuen Systems übernimmt aus dem zentralen ERP-System des Unternehmens die historischen Verkaufsdaten und teilt darauf aufbauend jeden Artikel basierend auf dem Nachfragemuster in ein so genanntes Bedarfsmuster ein.
Danach werden die zu erwartenden zukünftigen Nachfragemengen berechnet. Dabei ergibt sich bspw. für die gefragte Lederhose "Alpenglück" eine zu erwartende Nachfrage von 2700 Stück für den nächsten Monat.
Weiters hat die Lederhosen AG nun auch einen Überblick wieviele Artikel im Sortiment gerade einen steigenden oder fallenden Trend haben, oder eine hohe Schwankung in der Nachfrage. Dies verschafft einen guten Überblick.
Schritt 2: Inventory Optimization
Sobald wir den ersten Schritt, das Forecasting, erledigt haben, wissen wir mit welcher zukünftigen Nachfrage wir für jeden Artikel zu rechnen haben.
Nun wird es Zeit, die eigentliche Bestandoptimierung durchzuführen.
Dabei gilt es zunächst zu klären ob ein gewisser Artikel überhaupt auf Lager gehalten werden soll oder nicht. Die Praxis hat gezeigt, dass es nämlich keinen Sinn macht jeden Artikel auf Lager zu halten.
Die Faustregel lautet: je niedriger ein Artikel im Wert ist und je mehr Stück verkauft werden desto eher wird er auf Lager gelegt (Stichwort schnelldrehende C-Teile). Umgekehrt bedeutet das auch: je höher ein Artikel im Wert ist und je seltener er verkauft wird, desto weniger wird er auf Lager gelegt (Stichwort langsamdrehende A-Teile).
Ist entschieden ob ein Artikel auf Lager gelegt werden soll, geht es danach darum die wichtigen Bestandsparameter zu berechnen: Sicherheitsbestand, Bestellauslösezeitpunkt und optimale Bestellmenge.
Für diese Berechnungen sind unterschiedliche Informationen wie die vorhin bereits besprochene Bestandsart, der berechnete Forecastwert, die Lead Time und der gewünschte Lieferservicelevel nötig.
Nähere Details zu den unterschiedlichen Bestandsparametern erfährst du bald in einem eigenen Video.
Alles klar, sobald wir nun diese Parameter berechnet haben geht es weiter im letzten Schritt, in dem wir uns dann um die Beschaffung der fehlenden Mengen kümmern.
Praxis Inventory Optimization
Bei der Lederhosen AG wird mit den berechneten Forecast-Werten im nächsten Schritt, der Inventory Optimization, dann zunächst entschieden, welche Artikel überhaupt auf Lager gelegt werden sollen.
Dabei ergibt sich, dass die Lederhose "Alpenglück" ein höherwertiger Artikeln (A-Teil) ist und dieser auch schnell dreht. Diese sollen damit auf Lager gehalten werden. Ebenso sollten die Stutzen auf Lager gelegt werden, die schnelldrehende Artikel mit einem geringeren Wert (C-Teile) sind.
Hingegen sollte die Trachtenweste "Strittiger Oberförster" (A-Teil), die nur selten nachgefragt wird, nicht auf Lager gelegt werden.
Das Management der Lederhosen AG hat festgelegt für welche Kombinationen von Artikelwert und Nachfragemenge welche Lieferbereitschaft gegeben sein soll. Beispielsweise soll für die Lederhose "Alpenglück" eine Verfügbarkeit von 98% sichergestellt werden. Basierend auf dieser Vorgabe kann dann der Sicherheitsbestand, Bestellzeitpunkt und optimale Bestellmenge berechnet werden.
Schritt 3: Stock Replenishment
Sobald die Forecasts berechnet wurden, und darauf basierend die Bestandsparameter wie Sicherheitsbestand, Bestellauslösezeitpunkt und optimale Bestellmenge ermittelt wurden, geht es in den letzten Schritt: dem Stock Replenishment.
Nun ist zunächst zu prüfen, ob die benötigte Menge eines Artikels vielleicht aus einem anderen Lager des Unternehmens umgelagert werden kann.
Ist eine Umlagerung oder die Herstellung des Artikels durch eine unternehmensinterne Produktion nicht möglich so muss der Artikel von einem externen Lieferanten beschafft werden.
Dazu werden dann konkrete Bestellungen erzeugt, die an die Lieferanten gesendet werden können.
Praxis Stock Replenishment
Bei der Lederhosen AG sind nun die Bestandsparameter wie Sicherheitsbestand, Bestellzeitpunkt und optimale Bestellmenge berechnet.
Nun wird bspw. für die Lederhose "Alpenglück" geprüft, ob der nötige Bedarf im Hauptlager vielleicht durch ein anderes Lager abgedeckt werden kann. Und tatsächlich finden sich noch 50 Stück Überbestand dieser Lederhose im Lager eines Trachtengeschäfts in Innsbruck. Damit werden 50 Stück aus diesem Lager in das Hauptlager umgelagert. Die restlichen nötigen Stück werden, da diese Lederhose nicht selbst durch die Lederhosen AG produziert wird, als Bestellung an den Lieferanten weitergeleitet.
Zusammenfassung
Fassen wir noch einmal kurz zusammen...
Der Bestandsoptimierungsprozess besteht aus 3 Schritten. Dem Demand Forecasting, der Inventory Optimization und dem Stock Replenishment.
Im Forecasting werden basierend aus den Nachfragedaten der Vergangenheit die zu erwartenden Nachfragemengen der Zukunft prognostiziert.
Bei der Inventory Optimization erfolgt die eigentliche Bestandsoptimierung. Hier wird entschieden, ob ein Artikel überhaupt auf Lager gehalten werden soll und es werden Sicherheitsbestand, Bestellauslösezeitpunkt und optimale Bestellmenge berechnet.
Beim Stock Replenishment werden schließlich die fehlenden Mengen durch Umlagerung, interne Produktion oder externe Bestellung bei einem Lieferanten, beschafft.